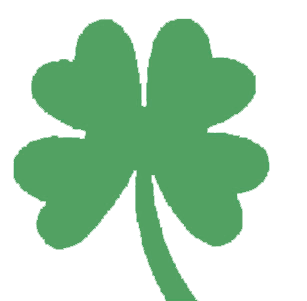
Dry ice blasting systems provide a superior clean. Designed with unrivaled innovation and unmatched performance, dry ice blasting systems let you clean better with less effort, increasing productivity and profit.
With the ability to shave any dry ice through patented feeder technology, new cleaning opportunities to suit your application’s need can be as gentle or aggressive as necessary – with blasting pressures ranging from 20 to 300 PSI – covering the widest range of applications in a single machine in the industry.
There are solutions for any budget with the widest selection of blasting machines and nozzles available anywhere in the world today. Whatever you need to clean, we can help you find the right solution for your application.
For more information about Dry Ice Blasters, visit www.coldjet.com
Below is great information about Dry Ice Blasting from http://wickensdryiceblasting.com/process/
Explanation of Dry Ice BlastingDry Ice or CO 2 Blasting is a relatively new cleaning process using solid CO2 pellets (known as dry ice). Dry Ice Pellets sublimate once they’ve hit the surface to be cleaned (convert directly from a solid blast pellet to a vapor) leaving a clean, dry surface with no residue. |
How Does The Dry Ice Blast Cleaning Process Work?
To use dry ice, the proper dry ice blasting equipment and dry ice blasting machines must be used. The Dry Ice Blasting process uses pellets made through a process of taking Liquid Carbon Dioxide (CO2) and expanding it to produce a snow like substance, that is compressed to make hard Dry Ice Pellets.
Dry Ice Pellets are then propelled at a supersonic speed by a compressed air gun (similar to other blasting systems). Upon impact, the dry ice creates a micro-thermal shock (caused by the extreme cold temperature of -79º C) which breaks the bond between the coating and the substrate. The high pressure air stream removes the dirt from the surface, while the Dry Ice Pellets vapourize (sublimate) before your eyes.
5 Reasons to use Dry Ice Cleaning
Reason #1: Increases uptime through in-place cleaning
The process is fast, thorough, and can be performed on-line without disassembly and without need for drying time.
Reason #2: Cleans without damaging the substrate
Dry ice blasting is non-abrasive. It quickly removes most contaminates without damage to switches, panels, lines, tubes, wiring or belts.
Reason #3: Reduces or eliminates the need for hazardous solvents
Dry Ice Blasting replaces chemical or solvent based cleaning and manual scraping.
Reason #4: Quicker and more thorough than cleaning by hand
Get a more detailed and quicker clean with CO2 by getting into tight spaced areas inaccessible by hand
Reason #5: Safe around electrical components
This versatile process cleans heavy industrial build up without damage to sensitive areas like electrical components, switches, wiring, photo electric sensors, etc
Dry Ice Blast Cleaning Comparison Chart
The Dry Ice Blasting process is superior to blasting with sand, glass beads and other types of cleaning methods for numerous reasons. As an Eco-friendly cleaning alternative, the dry ice cleaning method is quickly becoming favored for environmental as well as production reasons. Due to the nature of the Dry Ice Blasting process, there is no waste to be disposed of. Tremendous performance gains of little to no production downtime, quality of the clean, no clean-up, and minimized damage to equipment make Dry Ice Blasting a cost-effective cleaning option.
Dry Ice Blast Cleaning vs Traditional Methods
Blasting Cleaning Technique |
Waste for Disposal |
Abrasive |
Toxic |
Electrically Conductive |
Performance Comparison |
Dry Ice |
No | No | No | No | Excellent |
Sand |
Yes | Yes | No* | No | OK |
Glass Beads |
Yes | Yes | No* | No | OK |
Walnut Shells |
Yes | Yes | No* | No | Limited |
Steam |
No | No | No | Yes | Poor |
Solvents |
Yes | No | Yes | Yes | Limited |
* Each of these blasting materials becomes contaminated upon contact if used to clean hazardous objects. When that happens, these materials are then classified as toxic waste requiring safe and proper disposal. |